永洪社区
标题: 简单高效!制造企业降低维修成本要这样做 [打印本页]
作者: 寻找新技能 时间: 2020-7-22 11:18
标题: 简单高效!制造企业降低维修成本要这样做
随着科学技术的迅速发展,制造企业对设备维修从传统的被动维修转变为主动预防性维修。传统的维修方法主要基于已有的维修制度、基于运营中发生的各种故障、基于操作和检修人员的行业经验,在面对产品升级改造、设备从未发生的新故障,人工经验的欠缺等问题就会造成设备的过修或失修,其结果是维护费用的使用效率低,设备非预期的停机时间长,从而导致生产力损失与营运成本上升,也可能产生额外的维修与替换成本,使制造商必须准备许多零件,增加库存成本,最严重的还会带来重大安全问题。
在这种情况下,基于预测性维修的方式应运而生,通过预测性维修可以监控设备运行状态、定位故障原因、进一步对故障预测,确保质量,优化每一步资源,最大限度的减少非计划性维护停机时间,消除不必要的维修,节约成本、提高效率。
永洪科技产品Yonghong Z-Suite是融合BigData + BI + AI技术的一站式大数据分析平台,通过数据采集、数据治理、数据存储、数据挖掘和数据分析等过程洞察整个产品生命周期中各个时刻的状态和性能,并利用人工智能和可视化技术提供设备运行状态监控、故障根因分析、故障预测、决策分析全链条一站式应用解决方案。可有效降低设备全生命周期维修成本,实现预测性维修。
接下来介绍一下某风电巨头的一个真实案例,在某风电场中,风力发电机组出现了主轴承故障。主轴承是连接机组定轴和动轴的关键部件,主轴承发生故障轻则增加机组振动噪声,重则导致动轴卡死无法旋转。主轴承失效后只能更换无法修复,常见的故障分类包括磨损性故障、腐蚀性故障、断裂性故障及老化性故障。在风场中常用的故障检测方法多为定期维护,有时维护不及时就会造成比更换必要的零部件和人工成本更高的代价机组停机。因此建立提前预知主轴承故障模型,掌握主轴承运行状态是非常有必要的。
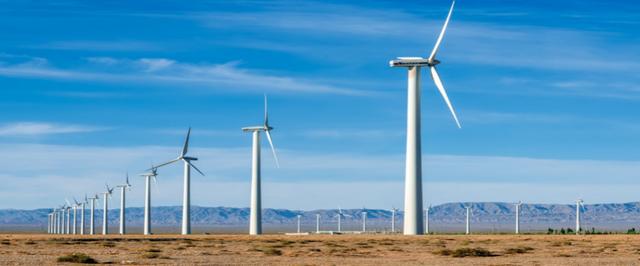
首先需从风场的传感器和SCADA系统中获取实时数据和故障文件数据,数据记录了风机的基本信息和风机故障的振动和温度信息,然后采用机器学习的方法建立故障预测模型,具体的流程如下:
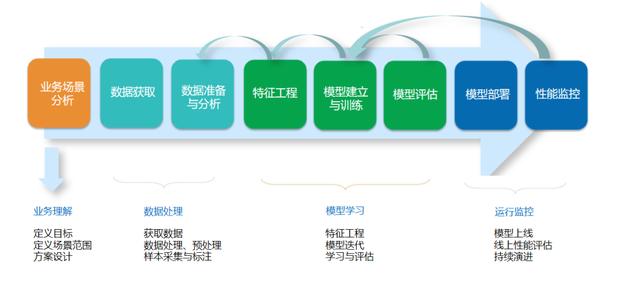
机器学习是一门人工智能的科学,该领域的主要研究对象是人工智能,特别是如何在经验学习中改善具体算法的性能。机器学习已广泛应用于计算机视觉、自然语言处理、生物特征识别、搜索引擎、医学诊断、检测信用卡欺诈等领域。机器学习的分类有很多种,但在企业应用场景下,多用监督学习和无监督学习。
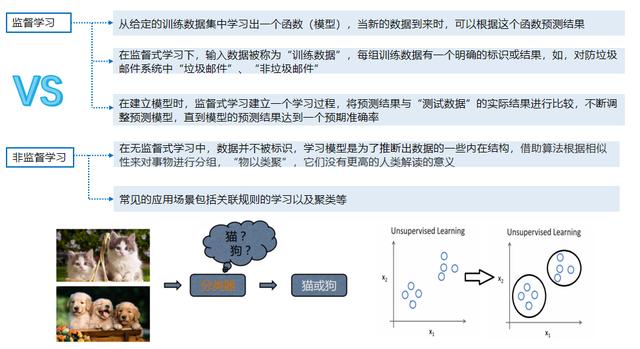
机器学习在制造业最典型的应用是设备故障预测,因此采用机器学习的方法来建立风机故障预测模型。首先进行数据预处理,将处理后的数据划分为训练集和测试集,对数据进行故障标注和探索分析,分析故障数据和正常数据的区别,发现故障数据在频域表现明显,因此以风速、转速、均值、方差、故障特征频率等为特征建立故障预测分类模型,方法可选择逻辑回归、随机森林、GBDT等,由于故障数据只记录了是否故障,没有记录故障位置,因此在建立模型时采用监督学习的二分类算法,模型建立完,可利用测试数据计算评价指标进行模型优化,选择效果最好的模型进行部署,最终上线的模型准确率可达90%以上,可有效的对故障风机进行预测,提前预知故障,减少计划外中断,增加设备综合效率,减少维修成本,提高产能。
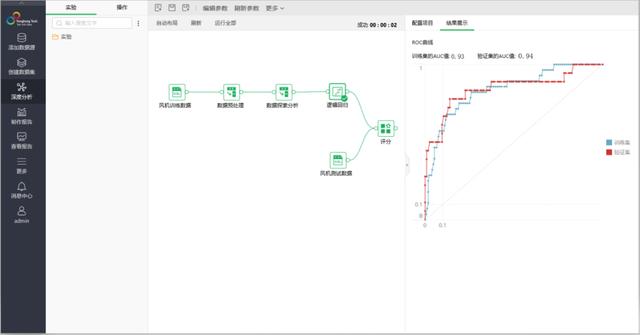
建模采用的是Yonghong Z-Suite的深度分析模块,通过拖拽即可实现从数据处理、建模、模型优化的全套流程。永洪科技Z-Suite产品作为新一代增强型数据分析平台,已在除故障预测外,包括出行预测、销售预测、库存优化、风险控制等多个行业和领域实现落地。
除了在风电上的设备故障预测应用,永洪在汽车行业也做了相关的故障分析应用。通过产品可视化可实现汽车设备状态监控和故障根因分析,如下是给某汽车公司做的IPTV目标达成分析,IPTV为每千辆车故障率,是汽车行业广泛应用的指标。首先选择不同的车型进行分析,确定对象后,可对具体车型查看IPTV目标达成分析状况和整车IPTV的状况,还可以查看具体的故障模式和责任部门,通过数据联动,查看故障发生问题时责任问题是分布在哪一个环节,从而在做对应的优化。
以上通过融合BI和AI的能力,有效解决了设备故障监控、故障根因分析、故障预测问题,最终帮助用户做出科学的决策。因此以融合BI和AI的新一代增强型数据分析将成为数据分析领域的一个新发展方向,能够帮助用户访问有效数据、探索数据,并对一些理论想法进行测试与验证,从而为分析带来更多的自动化功能以及创新洞察力。
欢迎光临 永洪社区 (https://club.yonghongtech.com/) |
Powered by Discuz! X3.4 |